First in a series
How a molecule changed the Gulf Coast — and the world
Ethane flowing from shale fields is triggering a petrochemical boom that’s reshaping markets
By Jordan Blum STAFF WRITER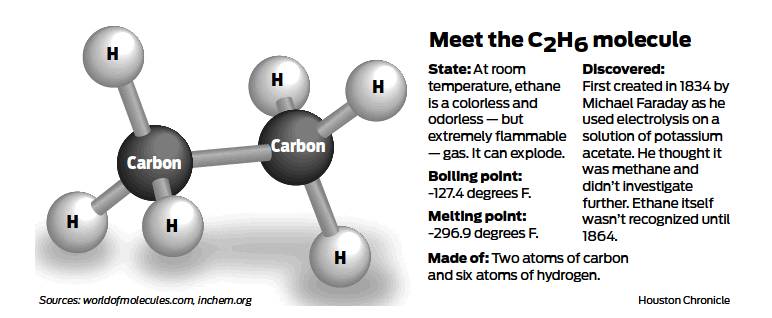
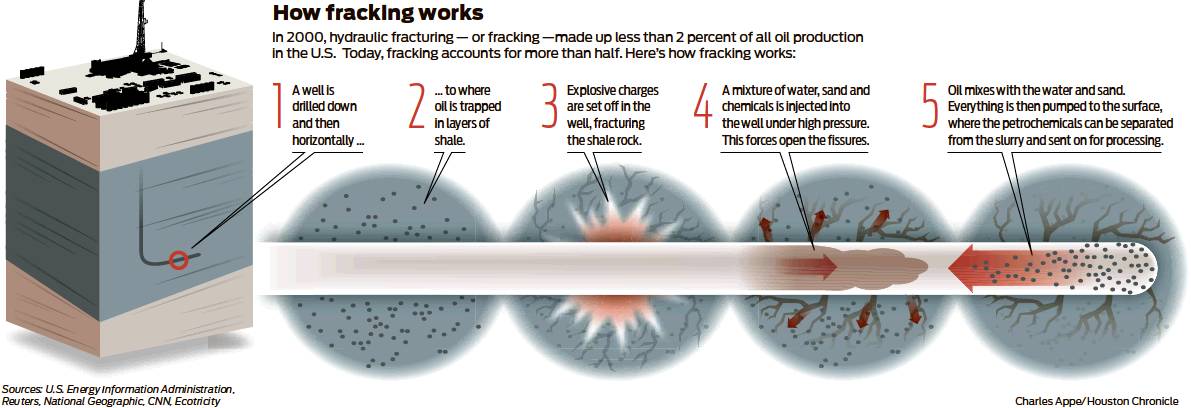
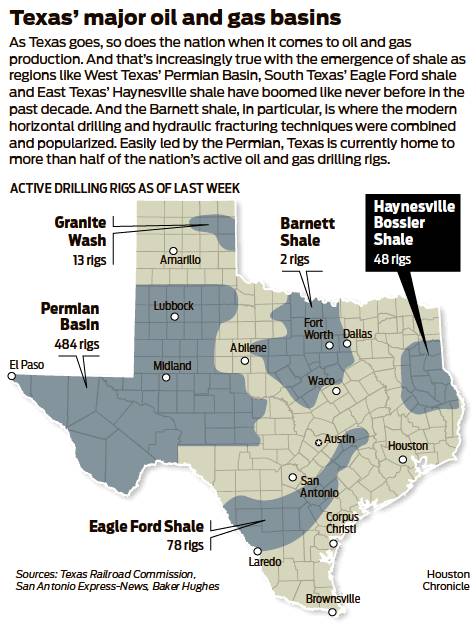
SAN AUGUSTINE — Working in nearly 100-degree heat, sweating through mud-stained coveralls, four roustabouts wrestled with 30-foot sections of pipe that would follow a drill bit plunging some 13,000 feet into the earth, then turning nearly 90 degrees to chew through another 10,000 feet.
Over the next few weeks, the well would be drilled, fracked and completed, freeing molecules of hydrogen and carbon that would rush through fissures in the dense shale rock and flow through the well as natural gas. But accompanying the natural gas particles was another, more complex molecule, containing two atoms of carbon each attached to three atoms of hydrogen.
That molecule, described chemically as C2H6, is transforming the Gulf Coast economy and reshaping global markets, from Europe to the Middle East and Asia. Known as ethane, the molecule is the catalyst for the petrochemical boom that has attracted tens of billions of dollars of investment, created tens of thousands of construction and manufacturing jobs, expanded exports, and fed the growing demand for consumer goods in China, India and other developing nations.
The impact of ethane is perhaps the most remarkable development in the remarkable story of the shale revolution. Less than three years ago, ethane was a largely unwanted byproduct of oil and gas drilling, much of it burned away in the natural gas stream flowing to power plants, businesses and homes, or flared off at well sites.
But today, ethane is feedstock for nearly half of U.S. plastics production and a valuable export to chemical companies around the world. As ethane flows from Texas shale fields, chemical and energy companies are building and expanding plants to take advantage of the cheap, plentiful raw material, plowing more than $140 billion into the Gulf Coast alone.
“It’s absolutely extraordinary this is happening in the United States,” said Neil Chapman, Exxon Mobil senior vice president. “I can assure you nobody predicted this in 2000 or even 2005.”
U.S. ethane production is projected to reach 2 million barrels a day by 2020, double the output at the height of the last drilling boom in 2014. On the journey from wellhead to market, ethane molecules will change forms several times as they are separated from natural gas, heated to become ethylene, processed into polyethylene, and ultimately extruded and molded into packaging and products that will appear on shelves in stores from Houston to Mumbai.
But it all starts here, at a natural gas well in East Texas.
Dancing with pipe
The Haynesville shale stretches across 9,000 square miles, straddling much of the Texas and Louisiana border. XTO Energy, a subsidiary of Exxon Mobil, began drilling the shale here a decade ago.
This particular drilling site is nicknamed Eagles — XTO names its sites after college mascots — and the well called Eagles DU #H1, the DU for drilling unit and the H for Haynesville. On a blistering July day, the 170-foot-tall rig had already made the turn from vertical to horizontal drilling, a gradual process that entails shifting at 10-degree angles every 100 feet until the bit travels sideways.
Oil field workers ran more pipe into the well, manipulating the rig’s 10,000-pound, hydraulically-powered tongs, called an iron roughneck, to screw the pipe sections together and drive them into the well. About 100 pieces of 30-foot steel piping laid next to the rig, each lifted by cables and guided by workers until it was vertical, awaiting the grasp of the iron roughneck.
“It’s kind of like a dance,” said Rick Cannon, an XTO vice president of production operations. “The pipe is pretty flexible, but you have to go slow.”
The Haynesville region was among the first shale formations exploited by the drilling and fracking techniques that spurred the shale revolution. Adecade ago, pioneering companies such as Chesapeake Energy of Oklahoma City and Petrohawk Energy of Houston began drilling the shale play to unlock natural gas reserves long thought to be inaccessible. XTO wasn’t far behind.
The U.S. Geological Survey estimates the Haynes-ville holds about 175 trillion cubic feet of recoverable natural gas, the nation’s second-largest gas reserve after the Appalachia region, which includes the Marcellus and Utica plays. Haynes-ville production hit a record 10.4 billion cubic feet of gas a day in 2011, fell to 6 billion cubic feet day in 2016 as natural gas prices plunged, but has since rebounded to 8.5 billion cubic feet a day.
As temperatures rose above 95 degrees, the men kept feeding the pipe to the rig, laboring through relentless heat and humidity. The work would go on 24 hours a day, in 12 hour shifts, interrupted only by mechanical failures and lightning, which can strike the tall, metal rigs.
Over the 40 days it took to drill the well, anywhere from six to 20 people worked at the site at any given time. Drillers and directional drillers piloted the process. Mud loggers monitored the geology, gas flow and drilling fluids. Floor-hands — better known as roughnecks — kept the drilling area and piping clean and organized. The company man, or well site manager, oversaw the operation.
Drilling pipe, which follows the drill bit and sets the well, would later be removed and replaced by casing pipe, cemented in place to line the well and give it structural stability, and tubing pipe, through which the oil and gas would flow.
Crews would test the structural integrity of the well and confirm that the volumes of hydrocarbons were sufficient to ensure the well would produce for years to come. About a month later, the fracking crews would get started.
Semi symphony
Less than a mile from Eagles well, past scattered small farms, lay another drilling site, called Fighting Camels, after the mascot of North Carolina’s Campbell University. Here, fracking crews were already at work.
The fracking site presented a deafening symphony of diesel motors. Dozens of semi-trucks powered the equipment that pumps millions of gallons of a water, sand and chemical mixture into the wells at high pressure, and dozens more trucks moved on and off the site delivering the water, sand and chemicals needed to crack the shale rock and release oil and gas.
The shale revolution is widely credited to the innovation and determination of one man, the late George P. Mitchell, son of a Greek immigrant and founder of The Woodlands. Mitchell, after striking it rich in oil, spent 35 years stubbornly focused on developing the Barnett Shale near Dallas, a play known once the “Wildcatters Graveyard.”
Mitchell, however, persisted, eventually combining hydraulic fracturing with horizontal drilling to unlock the complex shale rock. Mitchell didn’t frack his first profitable well until 1998, but with that success, he sold his company four years later for more than $3 billion to Devon Energy of Oklahoma City.
The shale boom was soon underway, producing oil and gas from Texas to North Dakota and the Northeast. It placed the United States among the world’s biggest energy producers, roiling global markets and upending more than 40 years of geopolitics .
And along with oil and gas came large volumes of another petroleum product known as natural gas liquids.
Three primary components can come out of any successful well: crude oil, natural gas, which is essentially methane, and natural gas liquids, primarily ethane, butane and propane. Ethane is the most prevalent natural gas liquid, or NGL, and used solely as a feedstock for petrochemicals.
In oil-rich areas such as the Permian, the NGLs flow out of wells as liquids in the stream of crude. In shale plays containing mostly natural gas, such as the Haynesville, ethane comes out as a gas, which is later separated from the methane.
At the fracking site, Tucker Energy Services of McAlester, Okla., led the operations for XTO. Workers, dragging heavy cables and chains, wore closed-channel headsets so they could hear each other, even from a few feet away, over the roar of the truck engines and other equipment.
Nick Cregan, a fracking field engineer with Tucker, was cooling off in the operations trailer as he prepared for the next fracking stage, the section of well that would get pounded by the high-pressure water, sand and chemical slurry.
Cregan travels here from his home in Oklahoma, nearly 300 miles away. He works two weeks on, one week off, spending too many nights in San Augustine hotel rooms while leaving his wife and four children behind. But the money is too good to pass up.
“It can be challenging and it’s tough work,” Cregan said. “There’s a lot of family time you miss out on. It’s hardly ever in your backyard.”
Beginning with a bang
Fracking begins with a bang — literally. Small explosive charges are lowered into the well, beginning at a depth of 200 feet, and detonated to create the initial fractures in the steel casing and shale rock. Next, the mixture of water, chemicals and sand are pumped into the well at a rate of 4,500 gallons a minute.
The sand, known in the industry as proppant, keeps the tiny fissures open; the chemicals help oil and gas to flow more easily from shale reservoirs.
The first wells fracked in the Haynesville shale consumed about 2 million gallons of water and 2 million pounds of sand. They were fracked in fewer than 10 sections, or stages.
The Fighting Camels well consumed 22 million gallons of water, most from privately owned ponds, and 16 million pounds of sand. Fracking crews targeted 52 stages, each a 130-foot section of the well.
The fracking proceeded with the efficiency of a factory. The sand went into a mixer where it was combined with water. Fracking chemicals were added to help lubricate the well and improve the flow of the slurry and the resulting production.
The pumping trucks then forced the mixture into the well and through perforations created by the explosions, shattering the shale rock and releasing the gas. “It’s like an assembly line — the water, sand, pressure pumps and the well,” said Buddy Davis, the Tucker Energy Services manager overseeing the site.
The Fighting Camels well began producing two months later, the Eagles well three months after that. Some of the gas flowed into pipelines that fed into Exxon Mobil’s English Bay pipeline system. Along the way, a processing facility separated the gas, essentially methane, from the natural gas liquids.
From there, the stream of natural gas liquids was piped to Mont Belvieu, about 35 miles east of Houston, where the ethane was separated from any other natural gas liquids. But it wasn’t the final destination for these hydrocarbon molecules.
It’s just the beginning of a transformation that is changing the flow of international commerce. jordan.blum@chron.com twitter.com/jdblum23